Bài viết này trình bày trường hợp điển hình về các bước áp dụng LEAN tại một nhà máy sản xuất thiết bị Dệt may. Nhà máy chuyên thiết kế, sản xuất và xuất khẩu các loại máy sản xuất ngành Dệt may. Việc áp dụng LEAN đã mang lại nhiều lợi ích kinh tế và xã hội cho công ty.
Để bắt đầu thực hiện dự án LEAN tại công ty, Ban lãnh đạo công ty đã cam kết áp dụng LEAN vào trong triết lý sản xuất của công ty và kế hoạch áp dụng được thực hiện theo ba giai đoạn.
Giai đoạn 1, khởi động
Bước 1: Nhóm dự án LEAN bắt đầu bằng việc tổ chức đào tạo cho Ban lãnh đạo công ty về LEAN và đưa ra một kế hoạch triển khai dự án LEAN nhằm giải quyết các vấn đề của công ty.
Bước 2: Dựa trên kế hoạch triển khai, nhóm dự án LEAN tiếp tục bằng việc đào tạo cho các cán bộ quản lý trung gian. Trong quá trình đào tạo này, nhóm phát hiện nhiều thách thức trong việc liên lạc, tuân thủ kỷ luật, thay đổi thói quen của cấp quản lý.
Bước 3: Khóa đào tạo tiếp theo được thực hiện với nhóm công nhân trực tiếp sản xuất, đó là nhóm có vai trò quan trọng trong tổ chức, nhóm được đào tạo về nội dung thay đổi nhận thức, thay đổi thói quen và quản lý nội vi trong nhà máy.
Giai đoạn 2, thực hiện
Bước 4: Nhóm bắt đầu hành động với việc việc Sàng lọc các đồ vật không cần thiết (đánh dấu đỏ vào đồ vật không cần thiết như máy móc, bàn ghế, linh kiện thay thế, tài liệu cũ, các sản phẩm lỗi thời). Qua đó bán thanh lý thu được 15 triệu đồng và giải phóng được nhiều không gian trống.
Ngoài lợi ích về kinh tế, hoạt động 5S còn nâng cao tinh thần của người lao động, vì người lao động thấy rằng công ty đang làm những việc có lợi cho mình như tạo ra môi trường làm việc an toàn, sạch sẽ hơn.
Giai đoạn 2 – thực hiện 5S giúp người lao động tham gia vào các hoạt động của dự án LEAN một cách tự nhiên, thông qua các hành động đơn giản của công cụ 5S, nhưng lại mang lại hiệu quả lớn về thái độ tích cực của người lao động với dự án.
Giai đoạn 3, sắp xếp lại dây chuyền sản xuất theo nguyên tắc LEAN
Không gian được giải phóng qua hoạt động sàng lọc với công cụ 5S được Ban lãnh đạo công ty sử dụng làm không gian bố trí lại nhà xưởng cho dự án LEAN.
Trước khi có dự án LEAN, công ty có hai phân xưởng lắp ráp sản phẩm (tự động và thủ công). Các sản phẩm trung gian được vận chuyển trong phân xưởng và giữa phân xưởng 1 và phân xưởng 2. Tuy nhiên, công ty chưa bao giờ nghĩ rằng có thể giảm được chi phí, và thời gian tại khu vực này.
Sau khi có dự án LEAN, công ty đã đưa ra giải pháp bố trí lại dây chuyền sản xuất (layout), sáp nhập 2 khu vực nhà xưởng, qua đó nguyên vật liệu và bán thành phẩm được đưa đến các công đoạn tiếp theo nhanh chóng và thuận tiện hơn. Giải pháp này được hình thành qua các bước thực hiện:
Nhóm dự án cùng với Ban lãnh đạo và người lao động bắt đầu thực hiện các giải pháp LEAN đối với phạm vi cả nhà máy, và tất cả các thiết bị theo dòng nguyên liệu và dòng thời gian. Theo đó, biểu đồ di chuyển nguyên vật liệu trong phân xưởng 1 và giữa phân xưởng 1 và phân xưởng 2 được vẽ ra để thảo luận hướng cải tiến. Sau rất nhiều thảo luận (brainstorming) ở nhiều cấp độ (nhân viên, quản lý, ban lãnh đạo) nhóm dự án LEAN đã đưa ra giải pháp sắp xếp lại công đoạn sản xuất.
Giải pháp cải tiến, bố trí lại dây chuyền nhà xưởng được trình bày trong 2 hình dưới, trong đó đường màu đỏ là đường di chuyển của nguyên vật liệu, bán thành phẩm tại phân xưởng 1; đường màu xanh tương ứng là đường di chuyển tại phân xưởng 2.
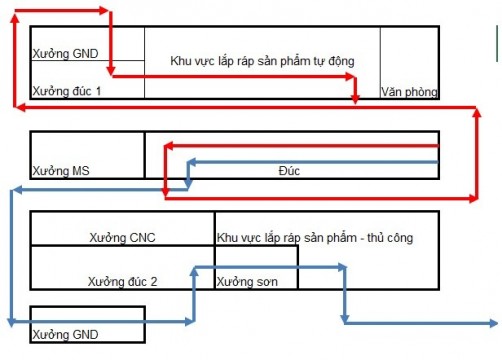
Trước thay đổi
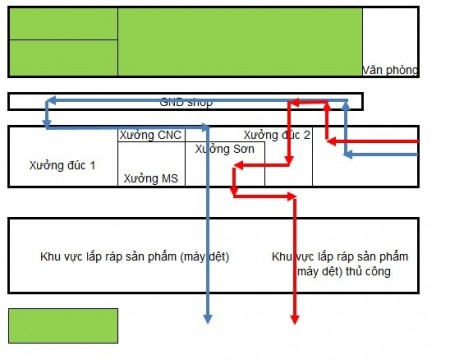
Sau thay đổi
Kết quả đạt được:
- Giảm được 40% không gian nhà xưởng (màu xanh trong hình trên).
- Giảm được 30% hàng tồn kho
- Thời gian làm việc tại xưởng đúc giảm từ 24 xuống 12 giờ
- Sản lượng sản phẩm tăng từ 24 lên 60 sản phẩm (máy dệt)/ngày
Như vậy, kết quả trên của công ty cho thấy vai trò của 5S và Lean trong quản lý sản xuất. Việc tập trung giải pháp vào các công đoạn sản xuất cốt lõi, là yếu tố chính giúp 5S và Lean mang lại hiệu quả lớn cho công ty.
Văn phòng NSCL