CNCPS Joint Stock Company is a unit with 12 years of experience in the field of mechanical processing and plastic injection. During the development process, the Company has constantly invested in many modern machines and technologies such as JSW, HUYDAI, HAITIAN, MAKINO, MAZACK, etc, to be able to provide high quality products to meet the needs demand of domestic and international customers.
With the aim of improving productivity and quality, from August 2019, the Board of Directors of CNCPS Joint Stock Company has sent the registration form to participate in the program to support the pilot application of overall performance management tool (TPM) for industry enterprises by the Department of Science and Technology, Ministry of Industry and Trade.
During the 4 months of joining the program (September 2019 to December 2019), the company had 9 working sessions with experts, and was instructed directly on the implementation of TPM. TPM activities performed at the plastic injection machine No. 6, factory No. 4 of the Company have brought about many practical benefits such as:
- In terms of productivity, quality and cost:
– OEE index increased from 51% to 78%
– Time for downtime due to malfunction has been reduced from 5400 minutes to 1296 minutes
– Number of dead time in a month decreased from 27 to 18
- For visual management: perform the visualization of oil tanks, pressure gauges, temperature, amperage and current voltage by color and color bars, written electrical control panels in Vietnamese in order to help the operator more easily recognize the viscosity level, easily identify the right or wrong voltage, temperature, intensity and voltage parameters, and understand the machine control functions. In addition, the 5S implementation is in the areas of raw materials (machine inlet), semi-finished products (output of the machine), where tools and auxiliary equipment make the working space of workers more convenient and professional.
- On manners and orderly: When applying the TPM, through daily reports of operators sent to the TPM group by Zalo, the QC staff monitors the quality ratio; Machine maintenance keeps track of machine performance ratios, and manager and machine operators monitor machine availability. Every week there are review meetings to rely on OEE indicators to analyze and propose solutions and improvements for machines.
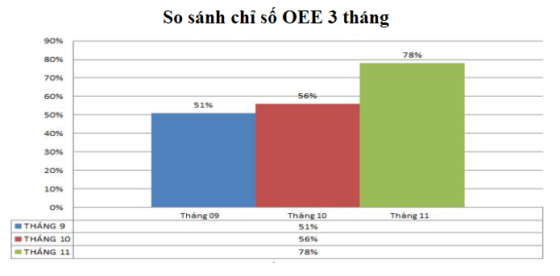
- Regarding production management: In order to apply the consulting TPM, it has guided 6 employees and managers of departments: two QC, two maintenance, two production, in the pilot area the machine No.6. The business leaders are very supportive and facilitate the TPM project board to function well, especially there are incentives when the TPM project committee has improvements to improve the OEE of the machine and plans to replicate the remaining machines right after the successful application of TPM for machine No.6.
- In terms of transport efficiency: The availability of tools and tools in the mold converter reduces the code change time also reduces the worker movement and benefits 30 minutes less than before the improvement.
- Regarding safety efficiency: The 5S improvement in the machine area, increasing the visual management of workers with machines, makes the working environment safer.
- Regarding training efficiency: The creation of 6 standards in the No. 6 engine area facilitates better operator, technical and maintenance instructions. In addition, the one-point lessons (OPL) are also a simple and effective approach to training workers, which are simple and easy for the trainees to understand.
The above achievements have shown the efforts and solidarity of all officials and employees in the organization. At the same time, this is also the driving force for the Company to continue applying the replication of TPM implementation for the remaining machines in the coming time.
Productivity and Quality Office