Case study at Goodman Fielder Bakery Malaga WA, 130 personnel
The company’s TPM results are summarized below, based on the results of the two TPM groups. The new company made a stage.
Group 1 – Bread Line Team
- Starting OEE was 38%, identified that potential OEE was 72% with two thirds of current losses caused by technical issues and one third caused by people development issues;
- Addressed issues of bread failing to traverse from the cooler to the packing conveyors saving $20,000 year in waste;
- Successfully piloted energy reduction ideas to eliminate the use of compressed air for non essential uses;
- Improved the plant ergonomics and reduced the risk of manual handling injury by eliminating lifting of grain
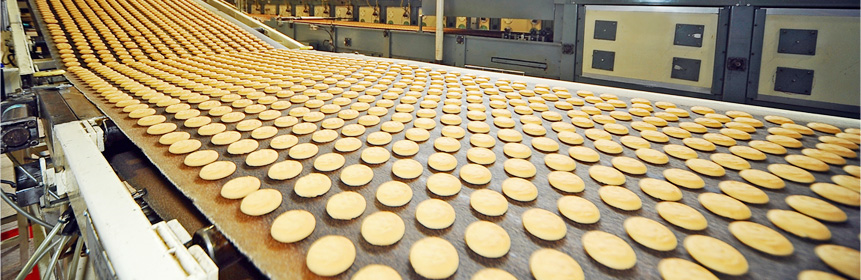
Group 2 – Roll Line Team
- Starting OEE was 25%, identified that potential OEE was 61% with half current losses caused by technical issues and half caused by people development issues;
- Introduced and established centreline settings to improve slicing and roll quality, reducing waste and customer complaints and credits;
- Eliminated the need for manual intervention to package cluster rolls reducing the risk of injury through improving the ergonomics; and Reduced incorrect receipting from 3000 units a day to less than 500 a week allowing the foundations of accurate data to plan
Case study at Goodman Fielder Dairy, Longburn NZ, 200 personnel
Cycle 1 Benefits:
- Implementation of the Fixed Production Plan for Milk Processing and Cultured Foods. This standardised weekly plan created stability and eliminated multiple changes to the plan;
- Improved OEE by 20% on the Beverages Filler 4 line through restoration and modification of equipment to make changeovers faster and more accurate, with less adjusting to ramp up to full production;
- Introduced packaging changes that improved productivity, reduced waste and yield savings over $29K per year;
- Improved the ergonomics of the pilot line operation and improve workplace safety; and
- Achieved excellent engagement of staff in the continuous improvement process.
Cycle 2 Benefits:
- Increased speed of the Filler 4 crate packer to match the filler speed and eliminate the need for hand Reduced the 500ml bottle giveaway loss saving $27,000/year;
- Restored and strengthened the Filler 4 cap applicator thus eliminating variability and identifying root cause and taking corrective actions to eliminate them going forward;
- Automated and simplified the paper streams required for managing the execution of the daily plan, which freed up Supervisors time for more value added activities;
- Created a design spec and layout for Cream Separator to reduce process variability of the new Separators, thus eliminate\ing the current fat give-away saving $150,000 per year; and
- Achieved excellent engagement of employees, in the continuous improvement
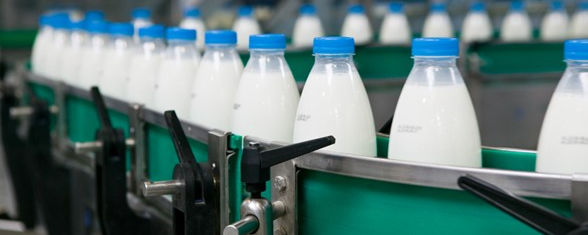
Cycle 3 Benefits:
- Improved the X-Mas custard output with over 300% more pallet movements and more than double the tonnage through the cooling tunnels;
- Developed the new separator design specification and room layout and the successful FAT checkout of the Stork Filler;
- Modified Micro 1 product conveyor and packing station heights to improve ergonomics and reduce Operator discomfort;
- Identified further fat, protein and water losses throughout Site and implementing solutions to reduce water losses and reclaim fat and protein for use savings over $170,000/year;
- Reduce product giveaway by establishing standard filler settings and investigating.
Productivity and Quality Office